Settling on the right shed construction material for your unique needs is a big decision when starting your build and there are many aspects to take into account. There’s always been a lot of ...
February 1st, 2023
7 min read
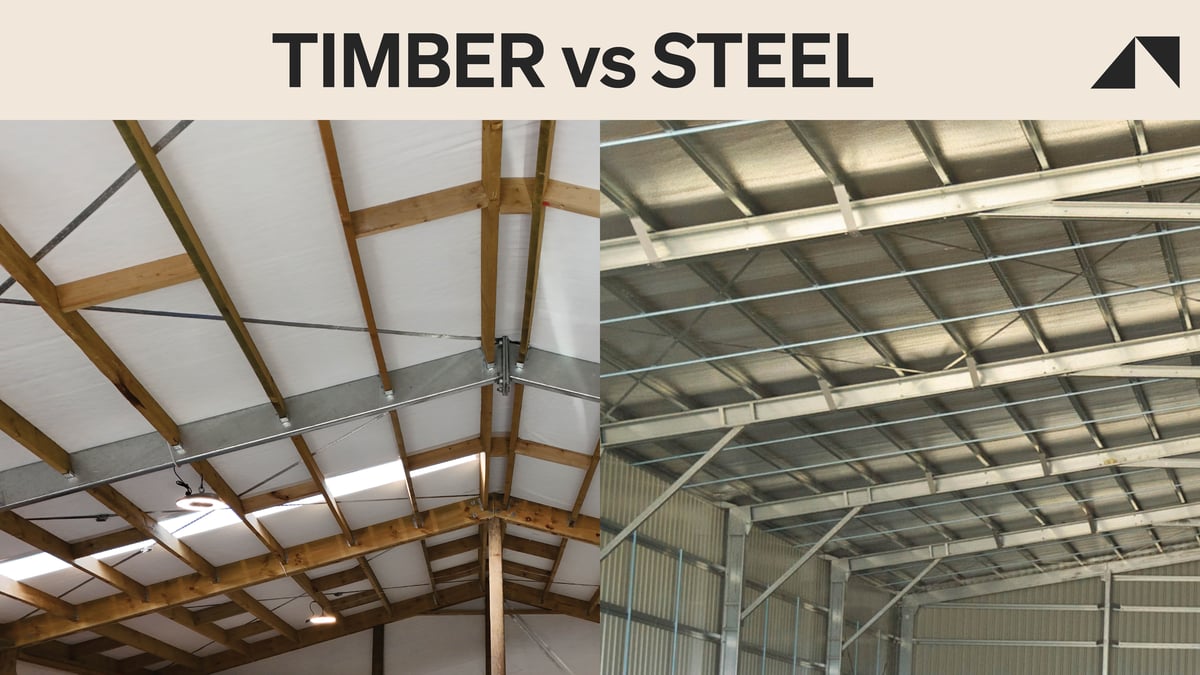